Getting My Alcast Company To Work
Getting My Alcast Company To Work
Blog Article
Some Ideas on Alcast Company You Need To Know
Table of ContentsAlcast Company for DummiesThe 15-Second Trick For Alcast CompanyAlcast Company Can Be Fun For EveryoneGetting My Alcast Company To WorkExcitement About Alcast CompanyThe 10-Minute Rule for Alcast CompanyThe Of Alcast CompanyAlcast Company Fundamentals Explained
It possessed great stamina and machinability. There are several various other light weight aluminum alloys that can be made use of for casting components. To figure out which alloys would certainly benefit your jobs, call Impro.

(AA), based in North America, has developed specs that regulate light weight aluminum alloys' make-up, homes, and classification. There are two kinds of light weight aluminum alloys functioned and cast.
The Single Strategy To Use For Alcast Company
Cast aluminum alloys are made by thawing pure light weight aluminum and incorporating it with other metals while in fluid type. The mix is poured into a sand, pass away, or investment mold and mildew. After solidification, the steel is gotten rid of from its mold and mildew. At this stage, it remains in either its final kind or as a billet or ingot for more processing.
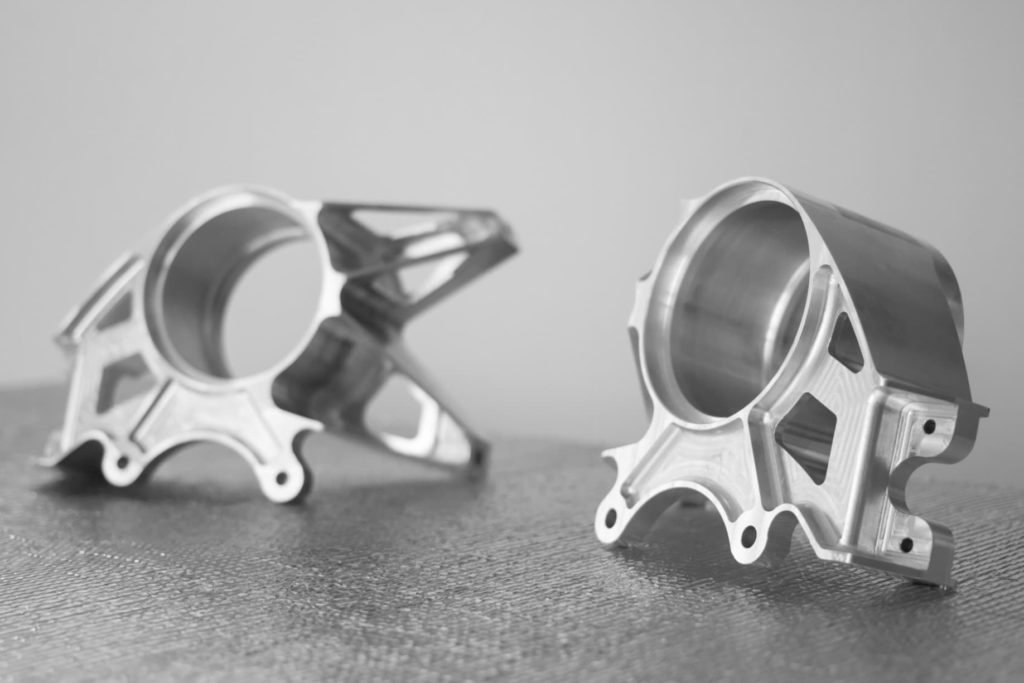
There are several small differences in between wrought and cast aluminum alloys, such as that cast alloys can consist of extra significant quantities of other steels than wrought alloys. The most significant distinction between these alloys is the fabrication procedure through which they will go to deliver the final product. In addition to some surface area treatments, cast alloys will certainly leave their mold in almost the exact strong form wanted, whereas wrought alloys will certainly undertake numerous adjustments while in their solid state
More About Alcast Company
If you think that a functioned alloy may be the finest for your task, have a look at some of our short articles that clarify even more about details functioned alloys, such as Alloy 6061 and Alloy 6063. On the various other hand, if you think a cast alloy would be better for you, you can discover more concerning some cast alloys in our Alloy 380 and Alloy 383 short articles (coming soon).
When selecting a light weight aluminum factory for your production requirements, it's vital to examine a number of factors. Among the most crucial elements to think about is the experience and capability of the shop. Selecting a foundry that has the best knowledge of the aluminum casting process, and the portfolio to show for it, assists to have a successful end result for your task.
The Best Guide To Alcast Company
Having the experience and industry knowledge to engineer your spreadings for optimal manufacturing and top quality results will enhance the job. Producing aluminum spreading needs a facility collection of processes to accomplish the best outcomes. When picking a new light weight aluminum shop to partner with, guarantee they have considerable market experience and are experienced regarding all elements of the light weight aluminum spreading process: style, manufacturing, product analysis, and item testing.
The foundry needs to also additional info have a tried and tested performance history of delivering phenomenal items that meet or exceed consumer expectations. Quality assurance must also go to the top of your listing when picking an aluminum foundry. By collaborating with a certified factory that complies with the standards for high quality control, you can shield the honesty of your product and guarantee it fulfills your specs.
Fascination About Alcast Company
By picking a firm that supplies solutions that satisfy or surpass your item requirements, you can be sure that your task will certainly be completed with the utmost accuracy and efficiency. Different parts need various production techniques to cast light weight aluminum, such as sand casting or pass away casting.
Pass away spreading is the name offered to the procedure of creating complicated metal parts through usage of mold and mildews of the part, additionally recognized as dies. It creates more elements than any type of other procedure, with a high degree of precision and repeatability. There are three sub-processes that fall under the category of die spreading: gravity pass away casting (or permanent mold casting), low-pressure die casting and high-pressure die casting.
Some Known Details About Alcast Company
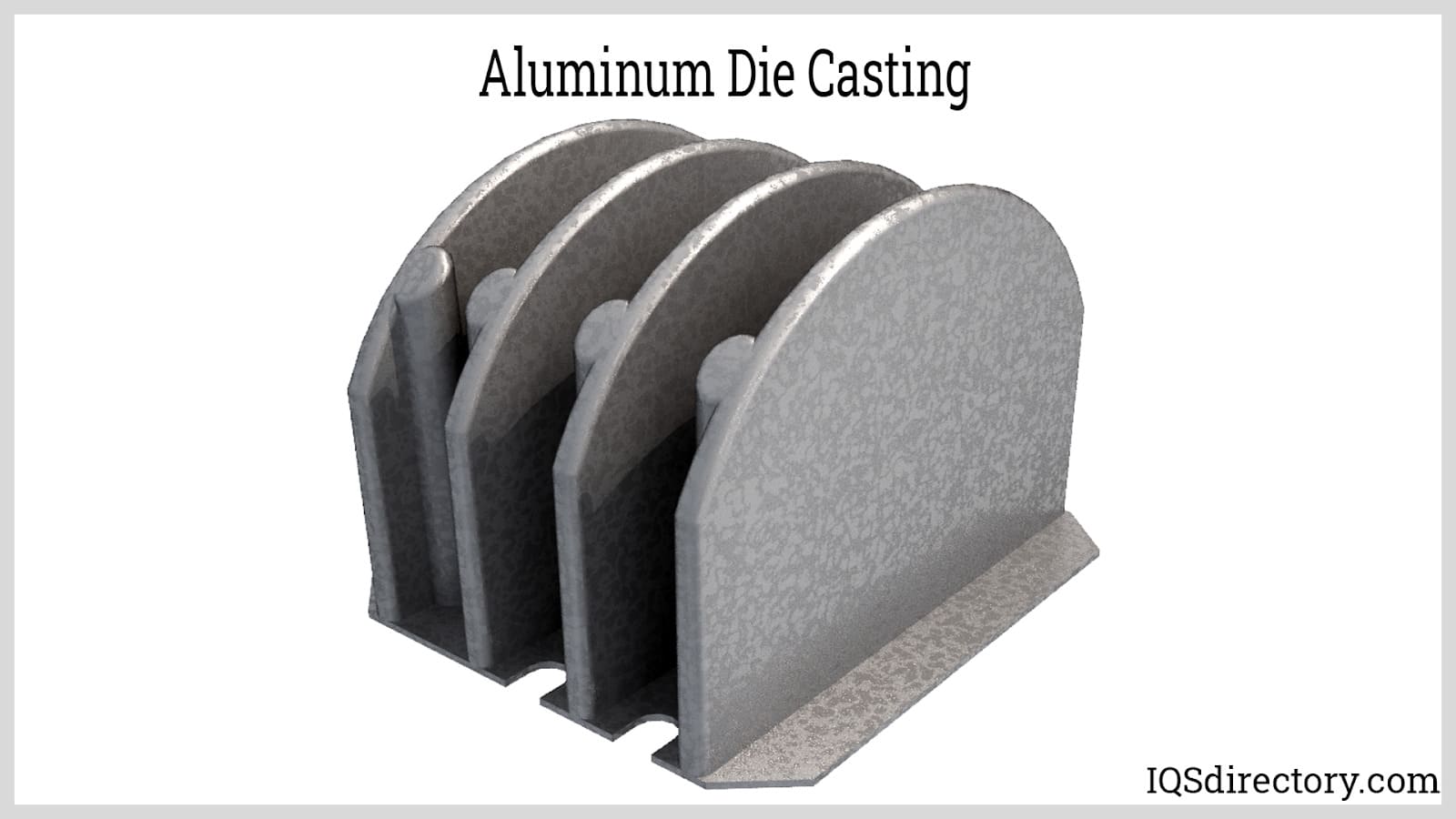
The pure metal, additionally understood as ingot, is contributed to the heater and maintained the molten temperature level of the steel, which is after that moved to the shot chamber and injected into the die. The pressure is after that kept as the steel solidifies. As soon as the metal solidifies, the cooling process begins.
The thicker the wall of the component, the longer the cooling time as a result of the quantity of interior metal that likewise requires to cool. After the element is fully cooled, the die halves open and an ejection system presses the element out. Adhering to the ejection, the die is shut for the next injection cycle.
Alcast Company Fundamentals Explained
The flash is the additional product that is cast during the process. This need to be trimmed off using a trim device to leave simply the primary part. Deburring removes the smaller sized pieces, called burrs, after the cutting process. Ultimately, the element is brightened, or burnished, to offer it a smooth surface.
However, this confirmed to be an unreliable examination, due to the fact that the tester could cut into a piece and miss a location with porosity. Today, top suppliers make use of x-ray screening to see the entire inside of elements without cutting into them. This enables them to extra accurately approve or reject parts. To get to the ended up product, there are three primary alloys made use of as die casting material to select from: zinc, aluminum and magnesium.
Zinc is one of the most used alloys for die casting due to its reduced expense of raw products. Its rust resistance also allows the elements to be long lasting, and it is one of the much more castable alloys due to its reduced melting factor.
Not known Incorrect Statements About Alcast Company
As mentioned, this alloy is one of one of the most typically utilized, yet manufactures will, at times, pick aluminum over zinc because of light weight aluminum's manufacturing advantages. Aluminum is extremely cost-effective and one of the much more functional alloys. Light weight aluminum is utilized for a number of different items and sectors anything from window structures to aerospace materials.
Report this page